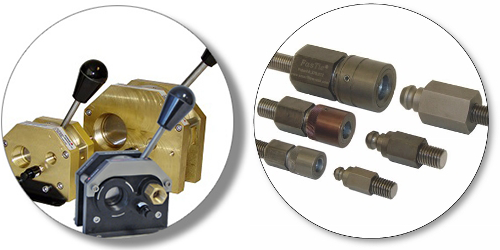
SMARTFLOW® SWAP Valves and FasTie quick ejector systems reduce changeover time related to ejector tie-in and water line removal by up to 90%, increasing the uptime of plastics manufacturing machinery for plastics manufacturers.
When it comes to plastics manufacturing, speed is everything. Without the right tools, manufacturers can face lengthy gaps in production during changeovers, and more, decreasing profitability and productivity.
With tools such as SMARTFLOW, SWAP Valves and FasTie quick ejector systems, injection molders can dramatically reduce mold change time for faster, more efficient workflows.
FasTie Quick Ejector Tie-In Systems
A FasTie system quickly “ties in” the mold ejector plate to the press ejection system within an injection molding press, helping to increase the speed of changeovers.
Ejector tie-ins are notoriously difficult without ease of access where ejector tie-in takes place. FasTie systems mount directly to the machine, minimizing mold change time with an easy, cost effective setup. The system is available in three sizes (1-inch, 1-3/8-inch, and 2-inch) and is ideal for most injection molding machines. A FasTie system is accessible and compact, and easily installs into existing molds and ejector plates with no additional machining required.
Traditionally, ejector rods are manually installed in difficult-to-reach areas. With this setup, changeover time can be lengthy, which results in time that the molding machine is not productive. The FasTie system automates the connection between the machine and the mold, alleviating the need for manual ejector tie-in.
Depending on the machine and molds, the FasTie system can save injection molders up to 90% of the time they would otherwise have to spend on tying in their ejector systems.
SMARTFLOW SWAP Valves
SWAP valves are simple and manually selectable valves that supply both cooling water to the mold during processing, and air to purge the water from the mold before a mold change.
These valves tie directly to the water systems that cool the molds and, like FasTie, easily connect to your existing equipment. With SWAP valves, manufacturers don’t have to worry about making a mess when changing over lines that are full of water. Instead, the valves purge the water from the lines prior to unhooking. The entire process only takes 2-3 minutes before all hoses can be disconnected.
SWAP valves bring speed and cleanliness to your manufacturing operations, transforming a task that was once time-consuming and labor intensive into an automated operation. Draining lines can be both messy and unsanitary for the work environment, creating a risk of slip and fall accidents and other safety hazards. With SWAP valves, plastic molders can have peace of mind in a fast, secure and clean operation..
Reducing Downtime from the Ground Up
SWAP valves and FasTie systems can provide up to a 90% increase in efficiency, cutting downtime between changeovers to a fraction of what it used to be.
At Plastixs, we work closely with our clients to ensure the solutions they invest in are tailored to their exact needs. If you’re not sure which tools are right for you, contact us and we can help you identify the best products for your business.
Contact us to learn more about decreasing injection molding changeover time