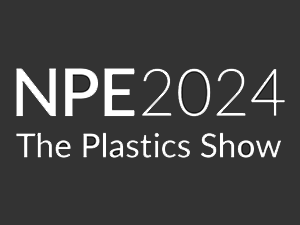
See Innovative Product Demos & Discover Solutions to Optimize Your Production Cell at Plastixs Booth S31027
Injection molding success comes down to maximizing the productivity of your skilled workforce and minimizing profit-killing interruptions – watch the video below to see how to solve these problems and what you’ll see at Plastixs at NPE2024:
Injection Molding Problems
- Leaks and equipment damage
- Lack of coolant flow
- Scale buildup and corrosion
- Product defects and scrap
- Downtime
- Injuries
The Opportunity
Bring us your problems and learn how to solve them so you can:
- Eliminate problems that can increase cycle time and decrease production
- Maximize the safety and productivity of your workforce
- Increase your throughput and profitability
Solutions
Visit Plastixs at NPE2024 to see the following innovative injection molding solutions firsthand:
- HiTemp Innovations: maximize your high-temperature molding investments, prevent leaks, and run safely with HiTemp manifold assemblies, hoses, fittings, and flowmeters
- Detect Plastic Leaks with AIRTECT: see a demo of how you can detect plastic leaks in hot runners and machine nozzles to prevent catastrophic damage – focus on prevention with the AIRTECT plastic leak detection system
- Moldshields: see a demo of how you can stop part contamination, defects and lost production with clear plastic mold side curtains that prevent parts from scattering
- X-FLOW Multi-Circuit Flow Validator: see a demo of how to validate and troubleshoot mold flow rate and temperature per circuit on up to 16 circuits simultaneously right from your iPhone, iPad or Android device
- Flowmeters & Flow Regulators: know your flow to reduce cycle times, balance flow, and detect cooling circuit clogs
- Hoses: see the best hoses for your applications, from HiTemp water/oil to plastic resin and other material handling hoses; includes Tigerflex, NORRES, Alfagomma, and more
Eliminate High-Temp Leaks, Part Defects & Injuries
High-performance, engineered plastics increasingly require mold temperatures up to 445° F to ensure they meet high quality standards and retain the correct material properties, particularly for aerospace, medical, automotive, and electronic/electrical parts.
High-Temp Problems
Conventional injection molding equipment is designed for use at a maximum temperature of 300° F (150° C) to prevent increased risk of leaks, part defects, and employee injuries.
High-Temp Solutions
Visit Plastixs at NPE Booth S31027 to learn how to overcome these challenges with HiTemp solutions, including manifold assemblies, hose, flowmeters, mold releases, lubricants, and more.
You can also download our new guide Solutions for High Temperature Injection Molding Cells, in which you will learn:
- Which hoses, fittings and manifolds are needed to withstand temperatures up to 445° F and beyond, and eliminate the risks of using softer materials like aluminum and soldered valves
- How to avoid glycol and ensure the purity of your water in open and closed loop systems
- About other important components used in high temperature applications
Missed Plastixs at NPE2024?
If you didn’t go to NPE2024 or didn’t have time to see us there, you can share your injection molding problems and find solutions by contacting one of our injection molding experts today.